Precision Matters: How Laser Cutting is Revolutionizing Aerospace Engineering?
In aerospace engineering, precision and efficiency are critical, influencing the success of projects ranging from passenger aircraft to military drones and space rockets. These designs must meet rigorous safety, durability, and aerodynamic standards. As the aerospace industry evolves rapidly, laser cutting aerospace engineering has emerged as a transformative technology, delivering unmatched precision, speed, and cost-effectiveness. By enabling the creation of complex, lightweight components with minimal waste, laser cutting not only enhances performance but also reduces production time, making it an indispensable tool for aerospace innovation and future advancements. This technology is setting new benchmarks in modern aerospace manufacturing.
The role of precision in aerospace engineering
Aerospace engineering is one of the most technologically advanced industries. Every component designed must be precisely manufactured and perfectly aligned to ensure maximum performance and safety. The structures of aircraft, satellites, rockets, and space probes consist of thousands of components that need to withstand extreme conditions – from intense aerodynamic and thermal forces to the low temperatures of the space vacuum.
In this context, precision is crucial. Even the smallest error in the execution of a component can lead to catastrophic consequences, putting both equipment and human lives at risk. This is why laser cutting aerospace engineering is gaining in popularity, allowing components to be created with minimal error tolerances and excellent quality. The technology’s ability to cut intricate shapes with high accuracy, while maintaining structural integrity, makes it a game-changer in the aerospace industry. Furthermore, laser cutting significantly reduces material waste and production times, making it both cost-effective and environmentally friendly, as aerospace manufacturers push for more sustainable practices.
Laser cutting is a technology that uses a high-powered laser light beam to precisely cut and shape materials. The laser beam melts, burns or vaporises the material where the energy is concentrated, allowing complex shapes to be cut with exceptional accuracy. In addition, an auxiliary gas (usually oxygen, nitrogen or argon) removes the resulting waste and cools the cut area, preventing deformation of the material.
With laser cutting, a variety of materials used in aerospace engineering can be processed, including aluminium alloys, titanium, stainless steel and composites. The technology makes it possible to process not only large panels and structural components, but also small and complex details such as microstructures inside jet turbines.
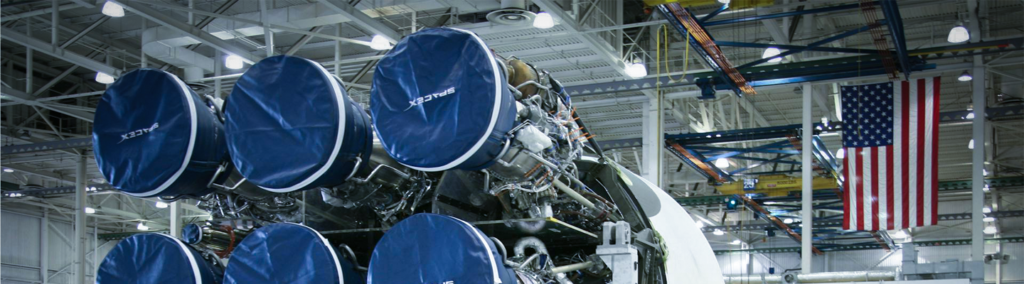
Laser cutting is widely used in various areas of aerospace engineering, helping to improve manufacturing efficiency and component quality. Here are some key applications of the technology:
Aerospace engine parts manufacturing
Aerospace engines, in both civil and military aircraft, must be manufactured with extreme precision to operate flawlessly under extreme temperature and pressure conditions. Laser cutting makes it possible to produce complex turbine and compressor components that must meet high technical requirements. With the laser, components with smooth edges and without material deformation can be achieved, which is crucial to maintaining engine performance.
Machining lightweight structural materials
One of the main goals of aerospace engineering is to reduce the weight of structures, resulting in lower fuel consumption and higher energy efficiency. To this end, modern lightweight materials such as titanium alloys and carbon composites are used, which are both strong and resistant to extreme conditions. Laser cutting is ideal for processing these materials, providing fast and accurate cutting without damaging the structure.
Production of satellites and rocket components
Not only structural components, but also aircraft interiors must meet stringent strength and safety standards. Laser cutting is used in the production of panels, seats and other interior components, ensuring precise cutting and a perfect fit of the components. What is more, the technology is also used in repairs, enabling damaged components to be cut quickly and efficiently.
Photo by Joerg Mangelsen : https://www.pexels.com/photo/commercial-airplane-maintenance-at-sunset-28513293/
Photo by SpaceX: https://www.pexels.com/photo/element-of-new-rocket-during-construction-at-factory-586093/