Laser Cutting Service.
Laser cutting is currently one of the most advanced methods of processing materials and has become extremely popular in many industries. From automotive manufacturing to electronics and arts and crafts, this is because the technology allows extremely precise and efficient cutting of a wide variety of materials such as steel, aluminium, copper, brass and even plastics. Thanks to the use of advanced laser systems, the process not only ensures accuracy at the highest level, but also saves time and material, making it indispensable in modern manufacturing.
What is laser cutting?
Laser cutting is a thermal process in which a laser beam is focused on the surface of a material, causing it to heat up, melt and vapourise. The laser emits intense light, which is focused using lenses to produce a very small point of high power density. When this point comes into contact with the material, the light energy is converted into heat, leading to local melting or even vaporisation of the material. At the same time, a gas (usually oxygen, nitrogen or argon) is directed at the cutting area to remove the molten material, leaving a precisely cut edge.
Types Of Laser Cutting Technology
There are several types of laser cutting technology, which vary in terms of application and the type of laser used. Here are the most popular ones:
- CO2 Laser Cutting
This is one of the most commonly used laser technologies. CO2 lasers use a mixture of gases (carbon dioxide, nitrogen, helium) that emit laser radiation with a wavelength suitable for cutting organic materials such as wood, plastics, glass, as well as metals. CO2 lasers are characterised by their high power and are able to cut thick materials with high precision.
- Fibre laser cutting
This technology uses semiconductor lasers that emit a laser beam through an optical fibre. Fibre lasers are more energy efficient than CO2 lasers and are ideal for cutting thin metals such as stainless steel, aluminium or brass. Due to their design, fibre lasers have a longer lifespan and require less maintenance.
- Nd:YAG Laser Cutting
This is a technology based on neodymium crystals that emit a very small diameter beam, ideal for precision cutting and engraving. They are mainly used in the electronics, medical and jewellery industries, where extreme accuracy is required.
Laser Cutting Applications
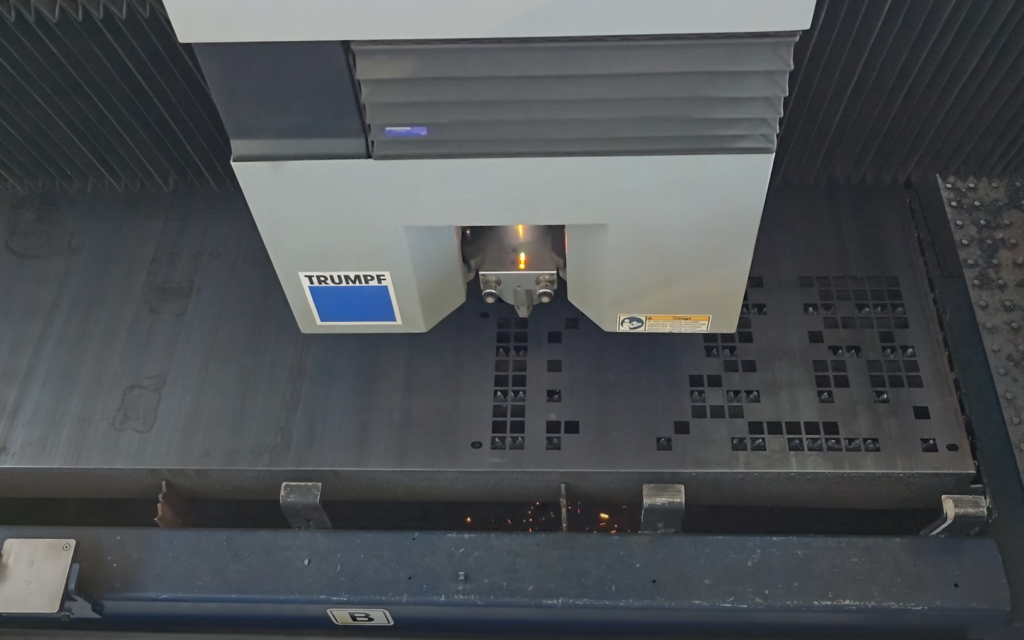
Laser cutting is used in many industries where precision, quality and efficiency are key. Among the key ones we can certainly include:
- Automotive – In car manufacturing, laser cutting is used to process bodywork, chassis components and internal parts. Laser cutting technology allows complex shapes to be cut quickly and precisely, which is essential in modern production lines.
Electronics – In the electronics industry, lasers are used for precision cutting of printed circuit boards (PCBs), housings and other components where minimum dimensional tolerances are crucial. With laser cutting, it is possible to achieve perfectly matched parts that guarantee the reliability of equipment operation.
Aerospace industry – High precision and the ability to cut difficult-to-machine materials such as titanium and composites make laser cutting widely used in the manufacture of aircraft and spacecraft parts. The technology makes it possible to create parts with complex shapes while maintaining high material strength.
Advertising and decoration – Lasers are commonly used to cut and engrave advertising materials such as Plexiglas, laminates, wood or metal. With lasers, it is possible to create intricate logos, letters or decorations that stand out with high quality workmanship.
Advantages and disadvantages of laser cutting
Like any technology, laser cutting has its advantages but also disadvantages, which should be considered before choosing the right method for material processing.
Advantages:
- Precision - Laser cutting achieves extremely accurate and clean edges, which is particularly important when producing parts that require a high quality finish.
- Efficiency - The speed of cutting and the ability to automate the process make it a very time-efficient method, resulting in reduced production costs.
- Minimal waste - The laser allows for maximum material utilisation, which reduces waste and is good for the environment.
- Versatility - The technology can be used to cut a variety of materials, making it a versatile tool in many industries.
Disadvantages:
- Capital costs - Purchasing and maintaining a laser cutting machine can be expensive, which is a barrier for smaller companies.
- Material limitations- Some materials, such as thick plastics and some metal alloys, can be difficult to cut with a laser.
- Safety- Working with lasers requires proper safety precautions and staff training to prevent accidents.