5 types of stainless steel - What is worth knowing about them?
Stainless steel is one of the most popular materials, used from construction and industry to the manufacture of tools and kitchen equipment. Its unique corrosion resistance and strength make it indispensable in many applications. Depending on its chemical composition and properties, there are several types of stainless steel, each with its own specific characteristics and applications.
For companies involved in, for example, laser cutting, choosing the right type of steel will be crucial, as it affects the quality and precision of processing. Therefore, below we will look at five basic types of stainless steel and their properties and applications.
Austenitic steel is the most commonly used type of stainless steel. It contains BOTH a high amount of chromium (16% to 26%) and nickel, which gives it excellent corrosion resistance. Within this group of steels, the most common are two varieties: steel 304 and steel 316.
Steel 304 is the most common type and contains approximately 18% chromium and 8% nickel. It is a steel with exceptional corrosion and heat resistance, making it an ideal choice for kitchen appliances, pipes and building components.
316 steel contains added molybdenum, which further increases its resistance to corrosion, especially in aggressive environments such as salt water. It is therefore widely used in the marine and chemical industries.
Austenitic steels are valued above all for their strength and flexibility, as well as their excellent corrosion resistance, even in harsh environments. For laser cutting companies, this type of steel is attractive in turn mainly because of its ease of machining and the possibility of achieving very precise cuts.
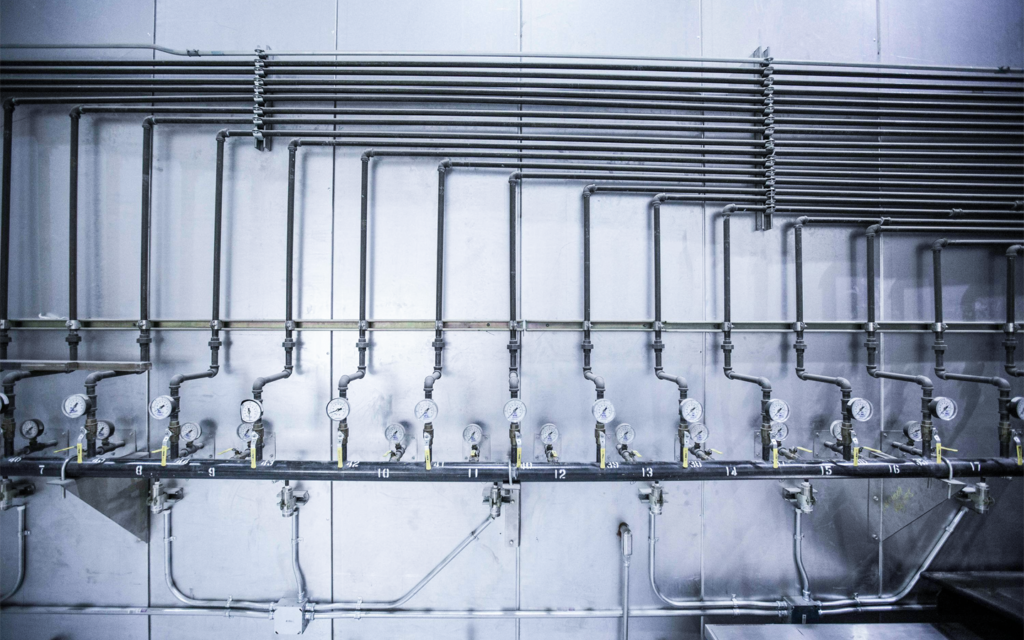
Ferritic steels are characterised by low carbon content (up to 0.1%) and high chromium content (from 10.5% to 30%). Compared to austenitic steel, ferritic steel is less resistant to corrosion, but has other advantages such as greater resistance to oxidation at high temperatures and lower cost.
The most popular grade in this group is 430 steel, which contains about 17% chromium. It is widely used in the manufacture of domestic appliances, such as refrigerators, dishwashers and ovens. Ferritic steel, due to its lower nickel content, is also more affordable, making it a popular choice in industries where material cost is an important factor.
When it comes to laser cutting, ferritic steel can be challenging as it is not as ductile as austenitic, which can in turn affect the quality of the cut. However, by properly adjusting the laser parameters, we will be able to obtain satisfactory machining results.
Martensitic steel is a high hardness stainless steel containing between 11.5% and 18% chromium and a relatively high carbon content. This type of steel is hardenable to increase its hardness and mechanical strength.
A popular grade of martensitic steel is 410, which is widely used for tools, knives, surgical equipment and turbine components. It is less corrosion resistant than austenitic steels, but its hardness and wear resistance make it indispensable where high mechanical strength is needed.
Laser cutting of martensitic steels requires fine-tuning of parameters, especially when the steel has been previously hardened. However, a properly configured laser can handle this material without any problems.
Duplex steel is a steel with a mixed structure – it contains both austenite and ferrite, which gives it unique properties. The chromium content of duplex steel ranges from 19% to 28% and the nickel content from 1% to 8%. This combination makes duplex steel extremely resistant to corrosion, especially in aggressive environments such as the chemical, marine and petrochemical industries.
Duplex steels combine the advantages of both austenitic steel (corrosion resistance) and ferritic steel (tensile strength and high temperatures). They are used in the manufacture of pipes, pressure vessels, pumps and heat exchangers.
Laser cutting duplex steel, like ferritic steel, is often a challenge because it is a high-strength material. It is therefore necessary to use a high-powered laser and to set the cutting parameters precisely.
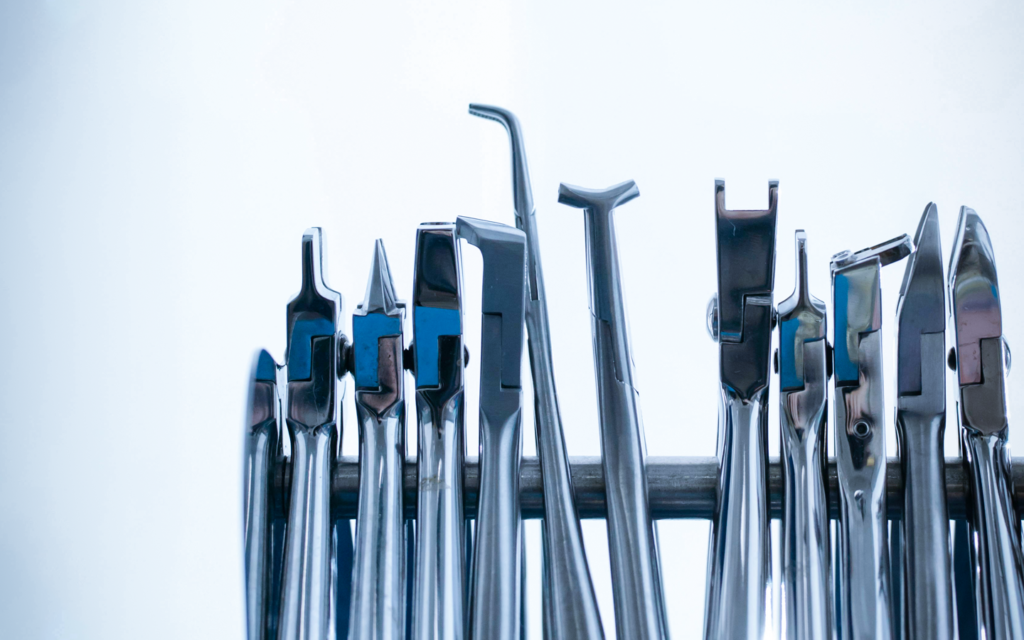
5. Precision steel
Precision (precipitation-hardened) steel, also known as PH steel, combines high mechanical strength and corrosion resistance. It contains chromium, nickel and copper, as well as additional elements such as aluminium, which allow for controlled ageing hardening.
Popular grades of this steel include 17-4 PH steel, which is widely used in the aerospace, defence and medical industries. PH steel has very high strength and hardness, making it ideal for applications requiring extreme durability.
Laser cutting of this steel requires high precision and power, but is possible with the right technology. Precision steel is often used in the manufacture of components where maximum strength with minimum weight is important, making it an extremely popular choice in the aerospace or medical industries.